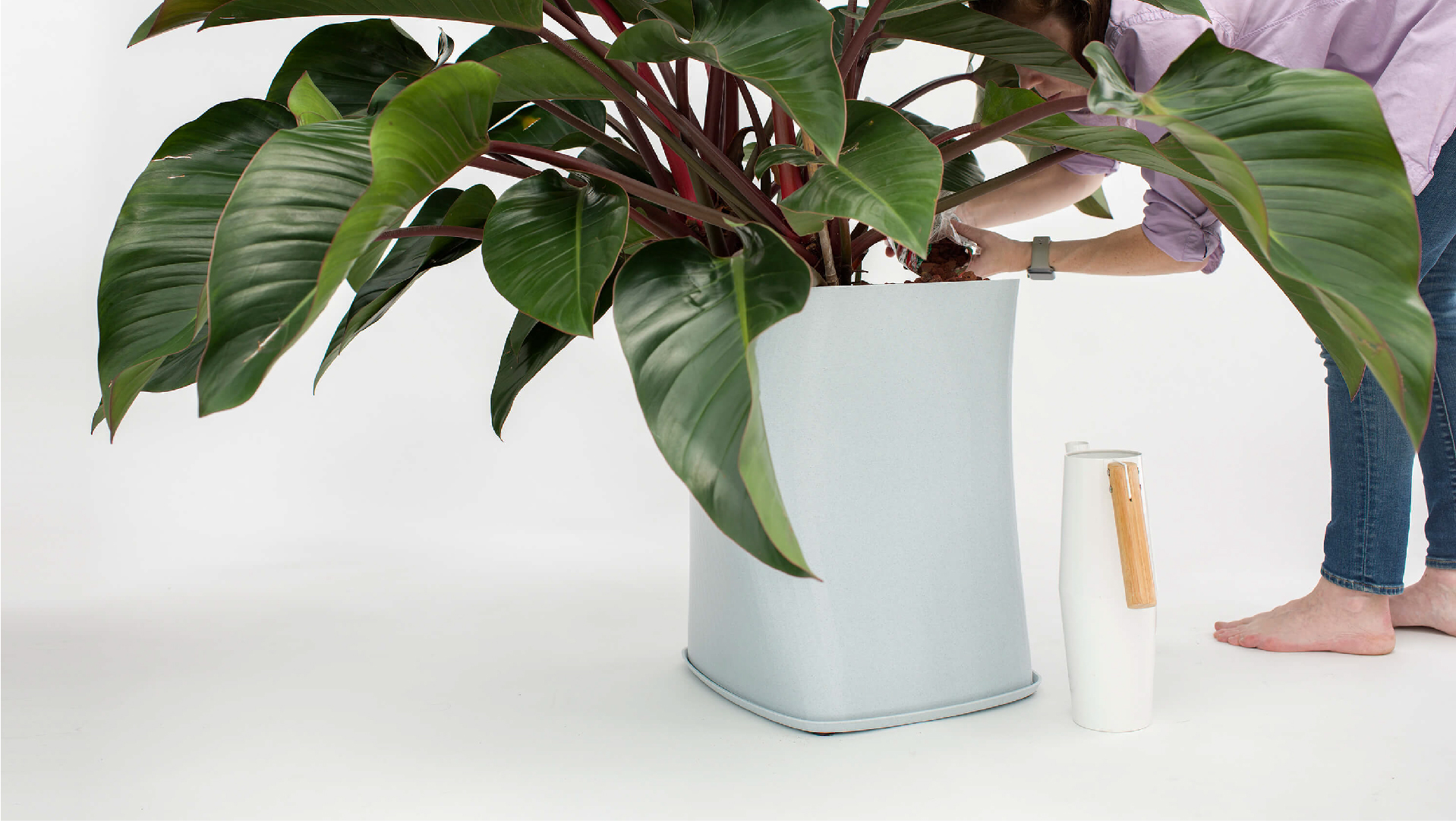
Model Nº is revolutionizing how furnishings are designed, produced and sold with their sustainable products and accessible prices.
It is no question that 3D printing technologies have changed the way things are made, and for Model Nº it is one of the many innovative processes that take part in producing their objects. With exciting new materials like an eco-neoprene made from tree sap and coconut leather, the studio develops high-quality furniture that gives a promising view of a circular future.
Reimagining the way costumers acquire their furniture, the company’s in-house 3D printing technology and digital fabrication allows them to deliver custom furniture on-demand in a matter of weeks using materials that are 100% renewable.
“Strata” coffee table by Model Nº
How did the journey for Model Nº begin?
Model Nº: “The furniture industry hasn’t evolved in decades although environmental and consumer needs have, consisting of items that are mass-produced with little original design or customization ability and are constructed from materials that are not sustainable or eco-friendly.
Model No. was founded by Jillian Northrop, Jeffrey McGrew, and Vani Khosla to solve these problems and reimagine how you can access sustainable artfully designed custom furnishings.
Model No. is revolutionizing how furnishings are designed, produced and sold. Our distinctive approach provides custom, sustainable products with accessible price points that are created on-demand by consumers. Model No. seeks to be the model for using the latest technology to deliver artful and accessible custom furnishings with zero waste.”
“Avens” chaise lounge by Model Nº
Model Nº revolutionizes how you can access sustainable artfully designed custom furnishings, could you tell us more about your design process, production, and what makes your practice sustainable?
Model Nº: “Model No. leverages in-house 3D printing technology and digital fabrication to deliver custom furniture on-demand in a matter of weeks using materials that are 100% renewable. Most furniture contains highly toxic materials such as flame retardant chemicals.
Model No. uses an innovative method of repurposing reclaimed wood and food waste. In the 3D-printing process, Model No. uses agricultural waste from corn husks, sugar cane and sugar beet as materials which minimizes carbon emissions and toxic by-products and are biodegradable.
Another point of difference, traditional non-custom furniture typically requires over 6 weeks for pieces to arrive at the customer’s home. Due to Model No.’s use of digital technology in the design and manufacturing process, our custom items arrive in the customer’s home in under 6 weeks.“
Model No. uses an innovative method of repurposing reclaimed wood and food waste.
Model No. is the first on-demand custom furnishings company driven by consumer needs and led by a devotion to technology, design, and environmental responsibility. In your opinion, how are manufacturers and consumers differently responsible when it comes to sustainable consumption?
Model Nº: “We believe it is both the consumer and manufacturers responsibility to produce and consume sustainable products. However, consumers are often not given the means to pursue sustainable purchasing as there are a lack of options available on the market.
Over the years, mass production as a result of the fast furniture trend has led to toxic emissions and an excess of unsold inventory made of materials that do not biodegrade. It is the manufacturers’ responsibility to provide consumers with the opportunity to purchase items that are not mass-produced, made sustainably, and customized to fit the consumers’ direct needs.”
Interested in more sustainable 3D printing projects? These are three manufacturing techniques pioneered by Supernovas.
In the 3D-printing process, Model No. uses agricultural waste from corn husks, sugar cane and sugar beet as materials
All your furnishings are made with sustainably sourced materials using the latest eco-friendly automated technology including 3D printing. How do you research and experiment with sustainable solutions for your products?
Model Nº: “We are constantly researching and keeping an eye out for new materials. It is a dynamic creative flow of what works well for the piece we are creating. In general, we use a lot of wood, aluminium and bio-resins. But we are also using leather, recycled leather, soy wax, cork and felt.
On the sidelines, we have exciting materials like an eco-neoprene made from tree sap and coconut leather that we hope to roll into some new products in the near future. Sometimes we find these materials on our own from doing research and sometimes our existing vendors bring them to our attention, knowing that we are always on the lookout for great new sustainable & eco-materials.”
“Atoll” credenza by Model Nº
Creating furniture with a devotion to technology, design, and sustainability, what material alternatives and new techniques do you think are the most relevant at the moment?
Model Nº: “For 3D printing, we use food waste such as corn husks, sugar canes, sugar beets, cassava to grind down into a PLA – Polylactic Acid – for it to be 3D printed. When looking for materials to use, we prioritize U.S. farms that have sustainable farming practices. For CNC fabrication, Model No. utilizes waste from by-products such as reclaimed wood which can be shaved down and repurposed for items such as Model No. ‘s tabletops.
3D printing and CNC fabrication are widely used in other industries; however, we are the first to adapt these technologies for use in the furniture industry. We harnessed these technologies to provide customers with the opportunity for on-demand customization, sustainable manufacturing, and shortened wait times.”
To reduce the carbon footprint Model No. has begun exploring creating micro-factories where products can be 3D printed in consumer hot spots.
What is next from Model Nº? What new projects are you working on?
Model Nº: “To reduce the carbon footprint caused from shipping items around the world, Model No. has begun exploring creating micro-factories around the U.S. where products can be 3D printed in consumer hot spots to aspire towards carbon neutrality.
While most mass furniture brands require large distribution centres and warehouses with excessive space to house overproduced furniture items, these micro-factories would only require a small area. Model No. plans to add recycling facilities in these spaces in order to take back used items.
Hinting at the company’s name ‘Model No.’, each product has its own individual model number, making it seamless to identify the type of material that the product was built with and the year it was manufactured which can then be broken down to raw materials to be repurposed through 3D printing. Imagine what was once a coffee table in your small apartment, could someday be an artfully designed credenza in your new dining room.”
Looking for more studios working with new materials and technologies? Check out the sustainable case study by Plasticiet.
“We believe it is both the consumer and manufacturers responsibility to produce and consume sustainable products.”
Clipped from: https://designwanted.com/the-model-for-sustainable-change-model-no/